The field of bulk material handling is undergoing a rapid transformation,driven by Industry 4.0 and automation trends.
From industrial automation to innovative pneumatic conveying system designs, these developments are reshaping the future of industries that rely on material movement.
MACTEX is at the forefront of this evolution, leveraging cutting-edge technologies to meet the shifting demand for efficiency, precision, and data-driven solutions.
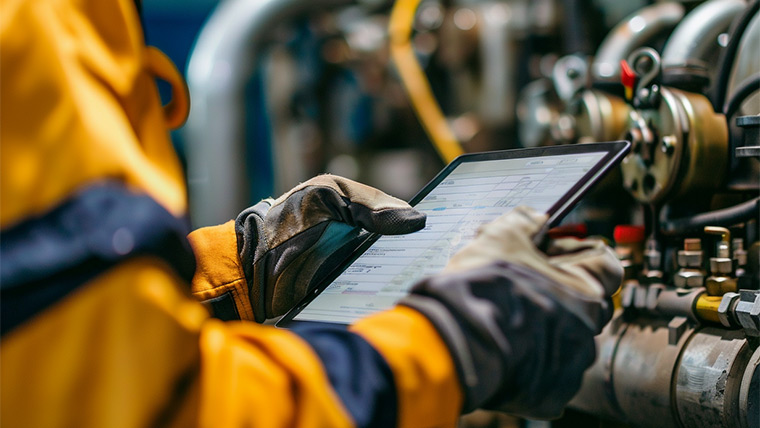
Here is a closer look at the latest pneumatic conveying trends to keep an eye on:
1. Automation
One of the most defining trends of 2025 is industrial automation, which allows for faster, more reliable operations, reducing manual intervention and enhancing overall efficiency.
Industrial automation integrates advanced control systems that utilise sensor feedback to operate valves, motors, and other components, streamlining processes and ensuring smooth material flow with minimal human intervention.
For example, automated loaders and unloaders in food processing ensure the precise and continuous transfer of powders like flour or sugar. These systems maintain consistent flow rates, prevent blockages, and reduce material loss, all while minimising labour requirements and improving operational efficiency.
2. Smart conveyors and data-driven systems
Smart conveyors represent the next step in material handling innovation. Equipped with smart sensors, these systems can monitor operational conditions in real-time, adjust performance, and alert operators to potential issues before they escalate.
In the pharmaceutical industry, smart conveyors equipped with magnetic detectors ensure precise handling and packaging of medications by detecting foreign materials.These conveyors can detect discrepancies in tablet counts, identify defective products, and segregate them automatically, ensuring compliance with strict regulatory standards while maintaining high throughput and product quality.
By collecting and analysing data, bulk material handling systems can make informed decisions to optimise throughput, minimise downtime, and reduce operational costs —enhancing efficiency and reliability.
3. Design innovation
Pneumatic conveying systems have long been a staple of bulk material handling engineering, offering an efficient and clean method for transporting materials through pipelines. Recent design innovations have taken these systems to new heights.
Modern designs focus on precision, reducing material degradation, and improving energy efficiency. For example, dense phase pneumatic conveying systems are ideal for fragile materials like food powders and pharmaceuticals, as they minimise damage during transport.
Automation in pneumatic conveying systems also allows operators to monitor and control the flow of materials remotely. This is particularly valuable in industries like food powder processing, where precise monitoring ensures hygienic handling, consistent material flow, and compliance with food safety standards.
With the global push toward sustainability, pneumatic conveying systems are also being designed with energy-saving features. For example, systems that recycle air or use low-energy blowers contribute to reduced energy consumption.
4. Internet of Things (IoT) capabilities
Industry 4.0 technologies, particularly IoT, are reshaping how bulk material handling companies approach their operations. These technologies bring real-time insights, predictive capabilities, and enhanced connectivity to the forefront.
IoT enables the interconnection of devices across a material handling system. Sensors embedded in equipment collect data on temperature, pressure, vibration, and other critical metrics. This data is then analysed to ensure optimal performance and identify potential issues.
For instance, IoT-enabled pneumatic conveying systems in food powder processing facilities monitor airflow, material velocity, and pipeline pressure in real-time. These insights help operators adjust parameters to maintain consistent flow rates, prevent blockages, and ensure the integrity of the transported food powder. By integrating IoT,such systems reduce contamination risks, improve energy efficiency, and enhance overall operational reliability.
5. AI-powered predictive maintenance
Beyond day-to-day improvements to efficiency, artificial intelligence (AI) is pushing the boundaries of predictive analysis and maintenance.
AI plays a pivotal role in predicting system failures before they occur. By analysing historical and real-time data, AI can identify patterns that indicate wear and tear, enabling proactive maintenance. Companies that use AI-driven maintenance report reduced downtime and extended equipment lifespan.
Coupled with real-time monitoring, bulk material handling operators are able to make informed decisions and quick responses to optimise system performance. For example, predictive maintenance and real-time monitoring in chemical processing plants ensures that hazardous materials are transported safely and efficiently, in a consistent manner.
As the experts in pneumatic conveying, MACTEX is committed to staying ahead of industry trends, offering innovative solutions with the latest technologies
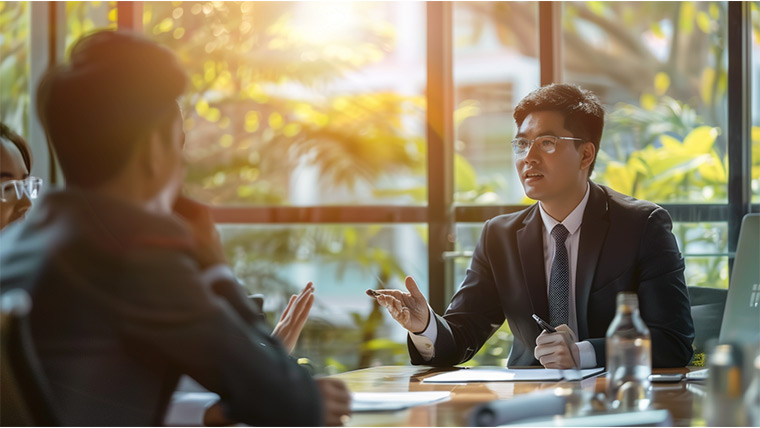
With a focus on automation in material handling, IoT, and intelligent systems, MACTEX is setting new standards in efficiency, precision, and reliability.
MACTEX’s innovative solutions include:
• End-to-end automation
MACTEX leverages automation forthe entire conveying process, from material unloading and loading to conveying, eliminating manual intervention.
This ensures high efficiency, precise operations, and lower labour costs, while reducing the likelihood of operational errors.
MACTEX’s pneumatic conveying systems also incorporate consistent flow rates and optimised energy usage. This is especially ideal for industries requiring consistent, high-volume material transfer with reduced dependence on manual oversight, such as pharmaceuticals, chemicals, and manufacturing.
• SCADA (Supervisory Control and Data Acquisition)
MACTEX systems also include advanced control and data management features such as SCADA, which provide real-time system monitoring, automated inventory tracking, and ERP integration.
Designed for industries requiring precise control and streamlined processes, SCADA allows operators to monitor pneumatic conveying systems in real-time, ensuring seamless operation.
Advanced inventory control tracks material levels with precision, eliminating stock discrepancies. The seamless integration with ERP systems also ensures streamlined workflows and accurate inventory management.
• AI and IoT connectivity
By incorporating AI and IoT, MACTEX provides real-time monitoring, control, and data analysis,enabling operators to remotely track system performance and monitor material flow rates.
In the event of blockages or faults in the system, MACTEX systems provide prompt issue resolution, ensuring minimal downtime. Thanks to predictive maintenance, operators can also prevent unexpected breakdowns and extend equipment lifespan.
In industries such as food processing, pharmaceuticals, and manufacturing, IoT-driven automation enhances operational efficiency by integrating performance data into user-friendly platforms. For example, operators can use tablets to view analytical dashboards displaying real-time data trends.
The future of bulk material handling lies in embracing the transformative power of industrial automation, pneumatic conveying, and Industry 4.0 technologies.
These advancements promise to enhance efficiency, reduce costs, and create more sustainable operations. By adopting advanced technologies like smart conveyors, IoT-enabled systems, and AI-driven predictive maintenance, companies can revolutionise their material handling processes.