What is Material Handling?
Material handling refers to the movement of dry solid materials from one location to another.
While the material handling process often involves bulk materials, ranging from powders to pellets. In cases like these, pneumatic conveying systems are often used to transfer dry solid materials in an enclosed pipeline via gas streams.
How pneumatic conveying systems can help with material handling:
Pneumatic conveying systems not only improve operational efficiency, but also ensure bulk materials are protected from contaminants and dust. The controlled atmosphere within these systems also help minimise wastage, leading to cost effectiveness.
Furthermore, these systems are flexible and can be adapted to fit existing plant structures. Scaling up or scaling down based on production needs is not an issue. Pneumatic conveying systems also utilise fewer moving parts, which means less wear and tear, leading to lower maintenance costs.
All in all, a well-designed material handling system is essential, as it can help optimise material handling workflow, maximise space, and uphold safety standards, ensuring reliable transfer of dry solid material. That is why it is important to work with material handling providers that have a proven track record and can provide tailored solutions, while integrating advanced controls and automated material handling solutions.
MACTEX Sdn Bhd specialises in solid bulk material handling. The company is an expert in designing and installing pneumatic conveying systems — this includes dilute phase and dense phase systems. They offer customised turnkey solutions to meet the diverse needs of different industries, while helping clients optimise the material handling process.
The established company provides world-class service, ensuring clients have peace of mind from the planning to the execution of every project.
Here are five essential tips to help improve the material handling process.
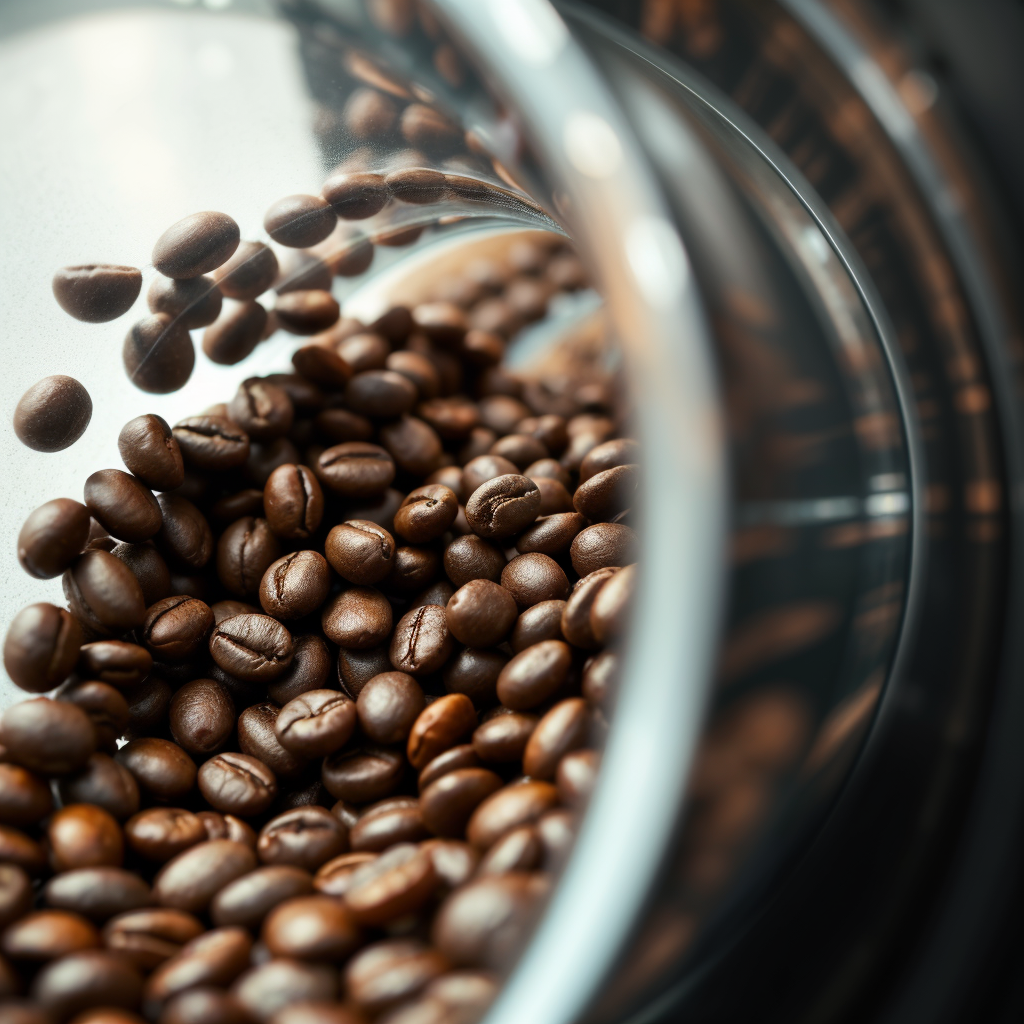
1. Start by evaluating material handling needs
The first step in improving material handling processes is by assessing the situation.
Whether it is installing a completely new system or making adjustments to the current one, there are a few key questions to explore:
- “Have you conducted a thorough examination of your current material handling process, including storage, transferring, and distribution?”
- “What obstacles do you encounter in the material handling process?”
To optimise the material handling process, it starts with understanding the existing procedure and analysing it to find potential areas of improvement.
The types of material and material consumption rate are key things to consider. It is important to prepare a detailed description of each material, including their rates, restrictions and different sub-handling processes.
Another crucial step is to consider the most critical conditions of flows and materials, which will ensure that the material handling system is able to cope with all demands required. If an elevated material flow is part of the system design, it is essential to account for increased capacity and maintain efficiency under all operating circumstances.
Lastly, evaluate all possible layouts and assess their upsides and downsides.
Pneumatic conveying systems are suitable for moving and handling dry solid materials without mechanical conveyors. Key components like blowers, feeders, and conveying lines allow these systems to optimise material flow and reduce manual handling.
Reach out to MACTEX Sdn Bhd for a thorough evaluation of material handling needs.
2. Choose the right type of system
Selecting the appropriate material handling system is crucial, with numerous variations even within pneumatic conveying to consider, such as dilute phase and dense phase systems.
Three important factors when designing a material handling system are: types of material, conveying distance, and sensitivity.
Types of material can range from powders, pellets, and granules, to other fluidisable materials.
Conveying distance refers to how far the materials will travel, as different systems are equipped to handle varying distances. Other considerations include horizontal or vertical applications and whether multiple inputs and outputs are needed.
Material characteristics is another crucial factor, as certain materials are abrasive and heavy, while others are non-abrasive and light, affecting the type of material handling system required.
Choosing the right system based on these factors will ensure minimal damage and maximum efficiency.
MACTEX Sdn Bhd offers a comprehensive range of pneumatic conveying systems and designs, including dilute phase and dense phase systems.
Dilute phase systems: These are ideal for lighter, non-abrasive materials. These systems can utilise both vacuum conveying and pressure conveying.
Dense phase systems: These are suited for heavier, abrasive materials, with vacuum and pressure conveying applicable for these systems.
3. Integrate advanced controls and process automation
Once a material handling system has been selected, the next step is to integrate advanced controls and automation technologies to significantly enhance system performance.
Advanced control systems such as programmable logic controllers (PLCs) manage and synchronise various components within a pneumatic conveying system. Variable frequency drives (VFDs) adjust the speed of electric motors, including blowers and compressors, to match the load.
Integrating advanced controls, coupled with sensors, actuators, and other control and data systems, allow for greater precision, process automation, and real-time monitoring in the material handling process.
When it comes to the human element, the simpler it is, the better. Simplifying and standardising the material handling process is crucial to reducing human errors and making better use of resources. For instance, human-machine interfaces (HMIs) provide operators with intuitive displays, immediate feedback, and alerts for quick resolution.
Automating material handling operations optimises processes, improves consistency and predictability, and reduces operational costs.

MACTEX Sdn Bhd provides state-of-the-art control systems that streamline operations, reduce human error through process automation, and elevate overall system responsiveness and reliability. Their systems also seamlessly integrate with DCS, SAP, and IoT platforms, ensuring comprehensive and efficient material handling automation solutions.
Reach out to MACTEX Sdn Bhd to find out how they can assist in providing material handling automation solutions.
4. Schedule regular maintenance and upgrades
Besides integrating advanced controls and process automation, another key aspect to improve material handling is by utilising predictive maintenance systems.
Leveraging data analytics, these systems help predict when maintenance is needed and prevent unexpected downtime. They can also schedule maintenance activities to coincide with non-peak times, minimising disruption.
There are various key areas of maintenance that one should be aware of, including checking for wear and tear, ensuring proper lubrication, and cleaning pipelines to prevent blockages. Proper and timely maintenance not only helps to avoid breakdowns and guarantee safety, but also decreases downtime and increases equipment longevity.
System upgrades, on the other hand, ensure that pneumatic conveying systems operate at optimal levels. Upgrading system components can lead to better performance and more efficient operations, using less energy to achieve the same or better results. Another purpose of upgrading is to enhance the system’s capacity to handle larger volumes of material.
MACTEX Sdn Bhd supports clients with comprehensive maintenance services — ensuring efficient and reliable pneumatic conveying systems — as well as system upgrades to adapt to evolving operational needs.
5. Monitor and optimise system performance
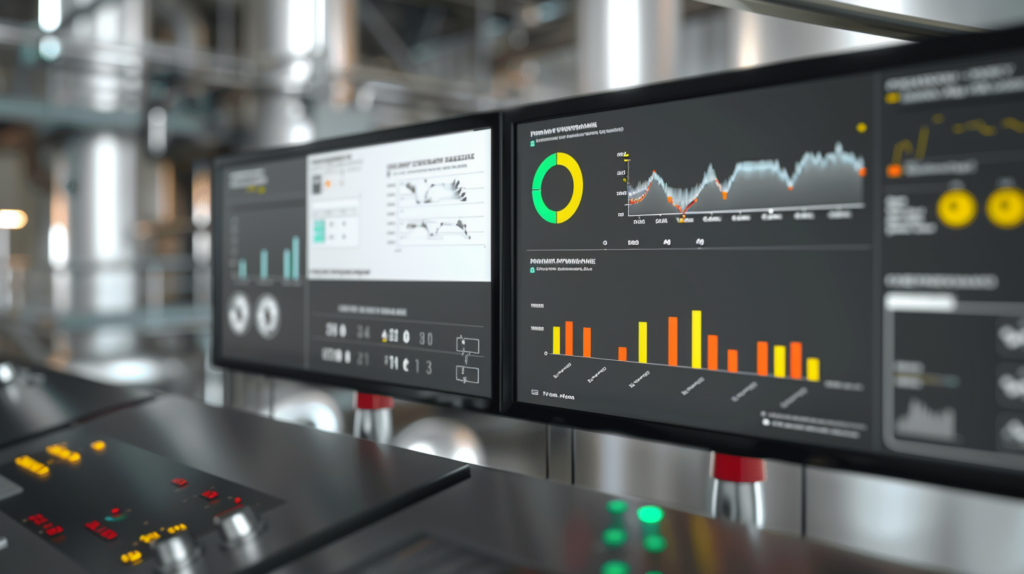
After implementing the necessary systems, it is essential for operators to regularly monitor and analyse data on system performance. Monitoring tools and performance metrics are vital for continuous assessment of pneumatic conveying systems and improvement of material handling processes.
MACTEX offers advanced monitoring solutions that help track key performance indicators and improve pneumatic conveying systems for optimised material handling.
For example, supervisory control and data acquisition (SCADA) systems can provide historical data analysis to help pneumatic conveying operators identify trends and optimise performance. These systems also trace material consumption, which provide valuable data to aid in optimising resource management.
In terms of areas to optimise, storage space is crucial. Designing storage areas and how materials flow through them go hand in hand. When storage space is maximised, it helps cut down the time it takes for materials to get from one place to another.
Improving the material handling process involves a comprehensive approach, and MACTEX Sdn Bhd’s expertise in pneumatic conveying systems makes it a leader in the field
Optimise material handling with MACTEX Sdn Bhd’s pneumatic conveying systems today.
MACTEX Sdn Bhd is well-equipped to assist every step of the way, from evaluating current needs, selecting between dilute phase and dense phase systems, integrating advanced controls and automated material handling solutions, scheduling regular maintenance, to continuous monitoring.
Ultimately, the key to a successful material handling system lies in ongoing improvement and adaptation to changing needs.
Reach out to MACTEX Sdn Bhd for a custom assessment today. Or, explore more about their technologies and services by speaking with industry experts.