How To Design An Energy Efficient Pneumatic Conveying System
Pneumatic conveying systems are the core of many industrial operations, ensuring the smooth and efficient transport of bulk materials.
That being said, when these systems experience downtime due to breakdowns or drops in efficiency, it can easily trickle into other aspects of operations, leading to production delays, increased costs, and decreased overall efficiency. Neglecting maintenance can lead to clogs, leaks, or motor failures, which disrupt production schedules and increase costs.
This is why implementing a robust preventative maintenance programme is essential for businesses relying on industrial conveyors.
From well-planned maintenance schedules to proper monitoring, companies can safeguard their systems while optimising operational efficiency and industrial reliability.
What is Preventative Maintenance and Why is it Important?
Preventative maintenance is a proactive approach to managing equipment, focusing on a series of scheduled activities designed to keep equipment in optimal condition.
These activities include routine inspections, cleaning, lubrication, and adjustments to prevent minor issues from escalating into major failures.
For pneumatic conveying systems, preventative maintenance is vital for:
- Avoiding Unexpected Breakdowns: Regular inspections can identify wear and tear early, reducing the likelihood of sudden malfunctions.
- Reducing Repair Costs: Addressing small issues promptly prevents the need for costly emergency repairs or replacements.
- Maintaining Operational Efficiency: Properly maintained systems operate at peak efficiency, ensuring consistent material flow and minimising energy consumption.
By prioritising preventative maintenance, businesses can significantly enhance the reliability of their pneumatic conveying systems while optimising their bottom line.
Discover MACTEX’s customised solutions, inclusive of scheduled maintenance services.
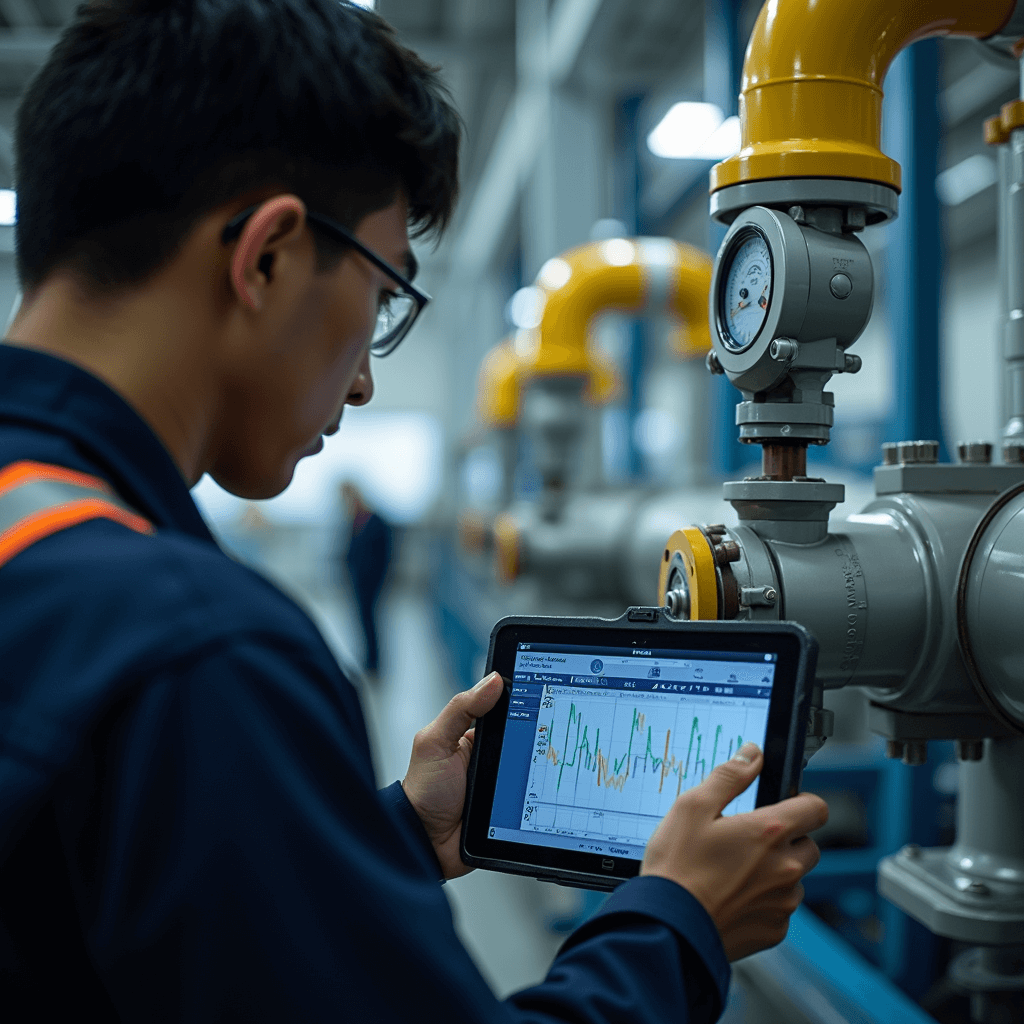
Key Warning Signs To Look Out For
Warning Sign #1: Increased Throughput Time
When pneumatic conveying systems experience a decline in efficiency, the time it takes to move materials from one location to another can increase significantly. This may indicate problems such as blockages, underperforming equipment, or airflow issues.
Warning Sign #2: Drops in Dispensing Volume Accuracy
Many industries rely on precise material dosing, especially when conveying powders or granular materials. A drop in the accuracy of dispensing volumes can be a clear indicator of an issue within the pneumatic conveying system.
This may be caused by factors like leaks in the system, blockages that reduce airflow, or malfunctioning components such as valves or feeders. Such discrepancies in dosing not only affect production quality but can also lead to wastage, potentially driving up operational costs.
Warning Sign #3: Leaks in the System
Leaks are one of the most common signs that your pneumatic conveying system requires attention. These can occur at any point, such as in the joints, connections, lines, and tubes. Leaks waste compressed air and blower air, increase energy consumption, and can lead to poor material flow, ultimately affecting system efficiency.
Warning Sign #4: An Increase in Operating Pressure
Fluctuations in pressure or vacuum can signal clogging or component malfunctions. Elevated pressure or vacuum levels can strain the system, leading to excessive wear, higher energy consumption, and potential system failure.
Monitoring pressure or vacuum readings regularly can help identify this issue early and prevent costly downtime.
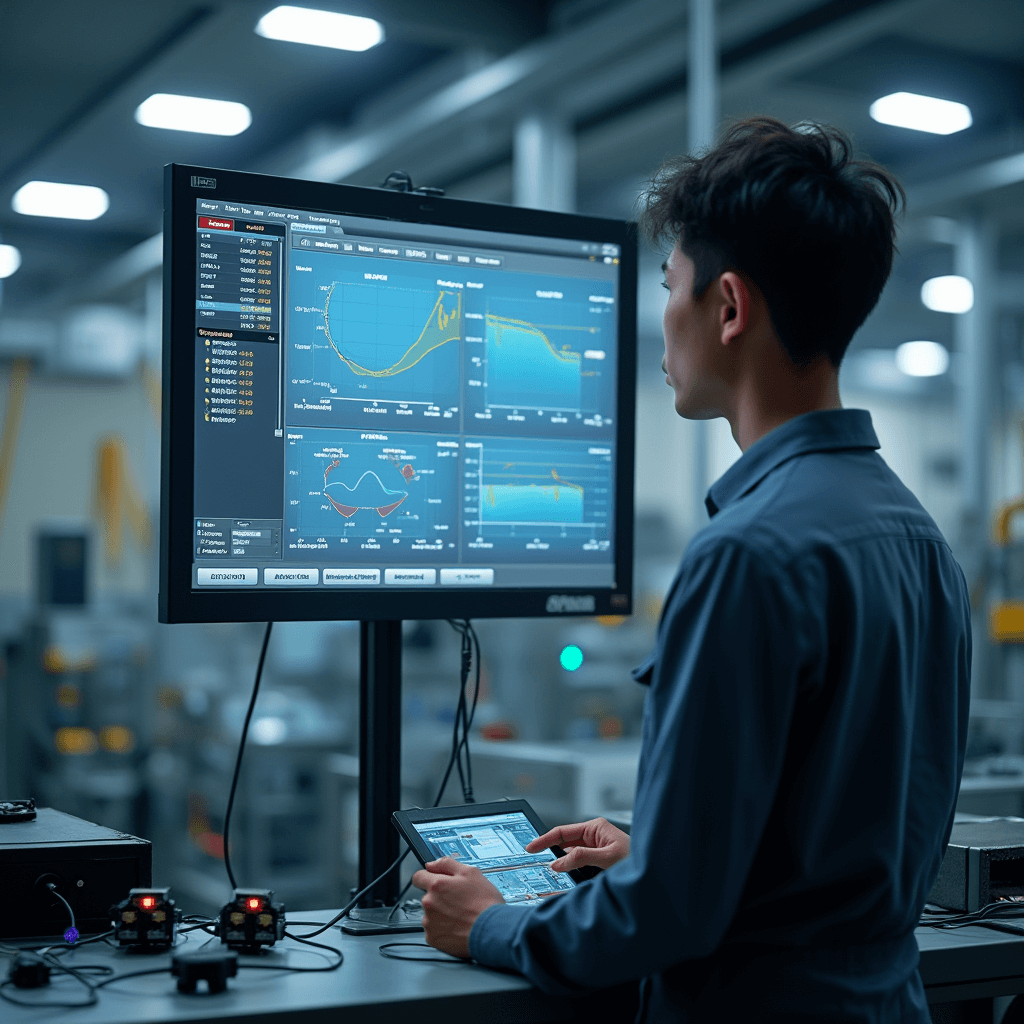
How To Maintain Pneumatic Conveying Systems for Long-Term Performance
No matter what is being conveyed in pneumatic systems, it will eventually start to wear down somewhere. By staying on top of preventative maintenance plans, operators will be able to catch problems while they are still small and avoid complete system breakdowns.
Properly maintained systems consume less energy and perform more consistently, leading to higher productivity. With regular maintenance, it also extends the lifespan of equipment and delays the need for costly replacements, leading to substantial financial savings.
Here are a few key tips when it comes to preventative maintenance for pneumatic conveying systems:
1. Create a schedule for equipment servicing, inspection, and maintenance
Preventative maintenance should follow a structured schedule, as some components require more frequent inspections than others. To ensure consistency and efficiency, consider creating an inspection checklist based on maintenance frequency:
- Monthly:
Grease all seals and check the ventilation and filtration systems on the blower. Clean these systems as needed. Inspect and replace wear parts, including filter cartridges, socks, metal cages, seals, and gaskets, to prevent operational disruptions. - Annually:
Lock out or tag out the entire system for comprehensive cleaning, servicing, and inspection. Inspect, clean, and test all components to ensure they are in proper working order. Replace consumable wear parts such as gaskets, seals, and filters as necessary.
Note: This checklist serves as a general guide. Every pneumatic conveying system has unique specifications and requirements, so always refer to the manufacturer’s guidelines and adapt the schedule accordingly.
2. Employ advanced diagnostic tools for performance monitoring and leak detection
Leaks in pneumatic systems result in energy wastage and reduced performance. Regular leak detection using advanced diagnostic tools can pinpoint areas of concern, allowing for timely repairs and preserving system efficiency.
Other than that, monitoring system performance helps identify anomalies, such as pressure drops or uneven material flow, which could indicate underlying issues. Continuous performance tracking ensures that any deviation is addressed before it impacts operations.
MACTEX’s automation, SCADA, and IOT solutions enable real-time monitoring and control over pneumatic conveying systems, ensuring timely detection of issues, efficient troubleshooting, and optimal system performance, minimising downtime and maximising operational reliability.
3. Ensure operators are well-versed with the system manual
The manufacturer’s system manual is an essential resource for preventative maintenance. It provides detailed guidance on servicing schedules, conveyor maintenance procedures, and troubleshooting steps.
Do keep in mind that while operators can perform basic maintenance, certain tasks require trained technicians.
Manuals also list essential spare parts, including wear-and-tear items and components with longer lead times, such as blowers, solenoid valves, and PLCs. Keeping these parts in stock reduces downtime during repairs.
Ensuring operators understand this information helps prevent excessive downtime by enabling swift action when issues arise.
As a reliable partner, MACTEX ensures pneumatic conveying systems are expertly designed, seamlessly installed, and properly maintained through comprehensive maintenance services
MACTEX offers a range of maintenance services aimed at prolonging the lifespan and productivity of pneumatic conveying systems, including:
- Customisable Servicing Plans: Tailored to meet the unique requirements of each system, ensuring optimal care and performance.
- Advanced Diagnostic Tools: Cutting-edge technology for accurate leak detection, performance analysis, and issue resolution.
- Expert Support: A team of skilled technicians with extensive experience in pneumatic systems, delivering reliable and efficient service.