How To Design An Energy Efficient Pneumatic Conveying System
In 2022, the industrial sector accounted for 37% of global energy consumption, according to the International Energy Agency (IEA), with this share expected to increase in the coming years.
Among the various contributors, material handling systems in industrial plants and warehouses stand out due to their substantial energy demands.
Devices such as forklifts, cranes, and conveyors play critical roles in operations but consume significant amounts of energy. Pneumatic conveying systems, in particular, require considerable energy to maintain the air pressure needed for moving materials through pipelines efficiently.
Designing energy-efficient systems is therefore essential not only to reduce operational costs but also to achieve sustainability objectives and minimise environmental impact.
Understanding Energy Consumption in Pneumatic Conveying Systems
Before delving into the design of energy-efficient pneumatic conveying systems, it is first important to understand how these systems function.
Pneumatic conveying systems use air or gas to move bulk granular materials and powdered products through a pipeline from one point to another.
These systems are highly effective for material transportation, offering advantages such as minimal environmental impact and reduced material loss within a closed system. In many cases, pneumatic conveyors can also outperform mechanical conveyors in terms of energy efficiency.
Despite their benefits, pneumatic conveying systems often have high energy consumption, influenced by several factors:
- Inefficient system designs, such as layouts with long pipelines, sharp bends, or unnecessary detours, significantly increase energy demand.
- Material properties like density, abrasiveness, or stickiness can also require more energy for transport, compounding the issue.
- Leakages and pressure loss further hinder efficiency, forcing systems to work harder to maintain material flow.
- Poor operational practices — such as running systems continuously under suboptimal conditions — lead to excessive energy use.
Addressing these inefficiencies is crucial to optimising energy consumption and enhancing overall system performance.
Discover more about how MACTEX’s energy-efficient pneumatic conveying systems can help to save costs, while improving production throughput.
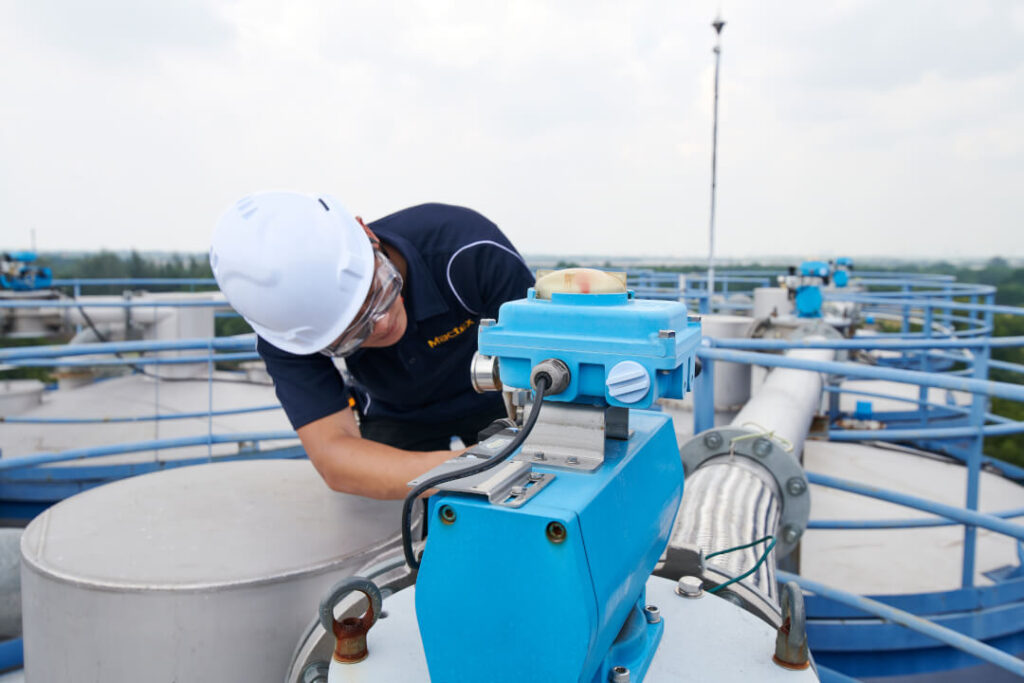
Key Design Principles for Energy Efficiency
Principle #1: Optimise airflow
Efficient airflow management is crucial to reducing energy consumption. Maintaining the correct balance between air velocity and material flow ensures that energy is not wasted on excessive air pressure.
Variable frequency drives (VFDs) and airflow control mechanisms can dynamically adjust the system to match operational needs, optimising performance.
Principle #2: Reduce pressure loss
Minimising pressure losses in the system is essential for energy efficiency. This can be achieved by designing shorter pipeline layouts, avoiding sharp bends and unnecessary detours, and using smooth, appropriately sized pipelines.
These measures help reduce resistance and the energy required to maintain material flow.
Principle #3: Consider material properties
The characteristics of the materials being conveyed, such as density, abrasiveness, and particle size, impact the energy required for transport.
Designing systems that accommodate these properties with tailored solutions — such as specialised pipeline coatings or customised airflow settings — enhances efficiency.
Principle #4: Incorporate advanced pneumatic conveying equipment
Operators looking to reduce energy consumption should consider investing in modern, energy-saving solutions.
High-efficiency blowers, compressors, and valves are designed to operate with lower energy demands. Additionally, using airtight seals and actuators prevents energy loss due to leakages, ensuring the system operates at optimal efficiency.
Practical Tips to Reduce Energy Consumption
Beyond design, operational improvements play a vital role in enhancing energy efficiency.
- Schedule Regular Maintenance: Conduct routine inspections and cleaning of all system components, including pipelines, blowers, and filters. Maintenance prevents clogs, reduces wear and tear, and ensures that equipment operates at optimal efficiency. Establishing a maintenance schedule can help identify potential issues before they escalate.
- Upgrade to Energy-Efficient Equipment: Replace outdated components with modern, energy-efficient alternatives. Transitioning to high-efficiency blowers, motors, and VFDs can significantly reduce power usage. Investing in equipment designed for low-energy usage often pays off quickly through energy savings.
- Implement Industrial Automation and Monitoring Tools: Utilise advanced sensors and automation systems to monitor energy usage in real-time. These tools can identify inefficiencies, such as excessive power draw or inconsistent airflow, and provide actionable data to optimise performance.
- Train Staff: Ensure that operators are trained in energy-efficient practices, such as shutting down equipment when not in use and recognising signs of inefficiency. Educated staff can help maintain optimal system operation and avoid unnecessary energy use.
By combining proactive maintenance with smart upgrades, businesses in various industries can achieve both immediate and long-term benefits.
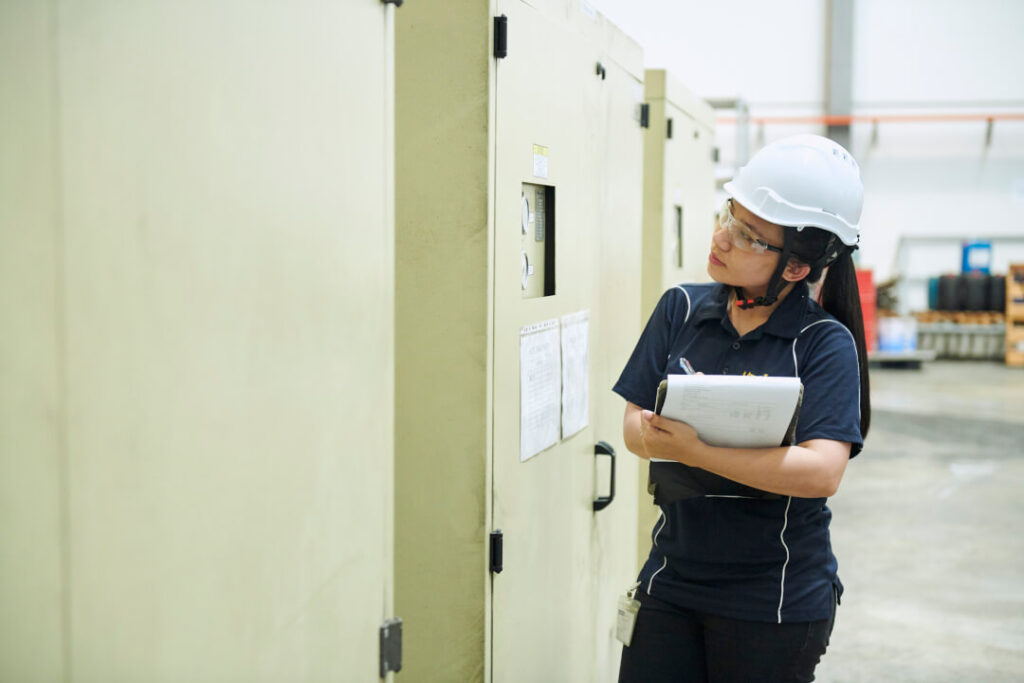
MACTEX is trusted for designing and building reliable, energy-efficient pneumatic conveying systems that deliver exceptional performance
From initial engineering and design to the procurement of top-quality materials, followed by precise construction and thorough commissioning, MACTEX’s EPCC process ensures optimal performance and client satisfaction at every stage.
As one of the best material handling companies, MACTEX’s advanced solutions include custom system designs specifically tailored to minimise energy loss while meeting specific operational requirements.
For instance, a manufacturing client reported a 25% improvement in production efficiency after transitioning to MACTEX’s pneumatic conveying solutions. Similarly, another client in the chemical industry reduced material degradation by 30% after switching to dense phase conveying.
All in all, improving energy efficiency in pneumatic conveying systems can lead to cost savings, enhanced sustainability, and reliable systems with uninterrupted operations.
By integrating innovative technologies ranging from high-efficiency blowers to automated control systems, MACTEX helps manufacturers reduce energy consumption, enhance productivity, and align with environmental goals.