Pneumatic conveying systems play a crucial role in material handling across multiple industries, including food and beverage, petrochemical, oleochemical, and minerals and ceramics.
These systems use air pressure in pipelines, transporting bulk materials in an efficient, enclosed, and automated manner.
While pneumatic conveying is a versatile solution for material handling, industries often face significant challenges stemming from blockages, system inefficiencies, and demanding maintenance requirements due to wear and tear, characteristics of raw goods, and environmental factors.
To navigate these obstacles, industries must keep their pneumatic conveying systems running smoothly to maintain energy efficiency, cost-effectiveness, and operational success.
MACTEX Sdn Bhd troubleshoots the top pneumatic conveying problems and provides actionable solutions to overcome them.
This way, businesses can optimise their material handling, reduce downtime, improve cost savings, and enhance energy efficiency.
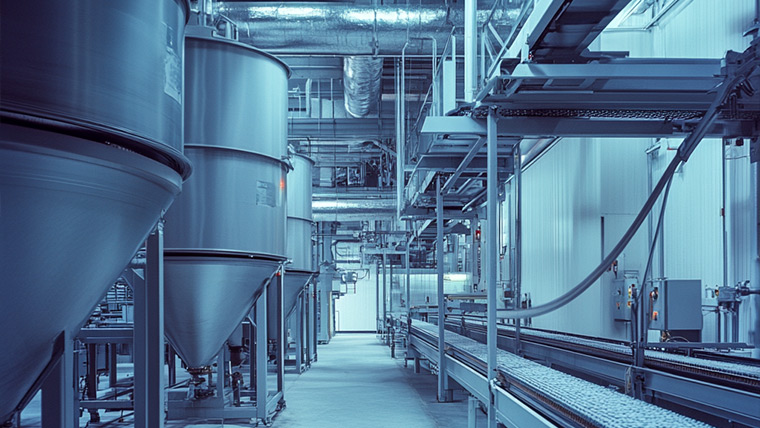
Common Challenges in Pneumatic Conveying Systems
• Blockages and Material Build-Up
One of the most common and disruptive challenges in pneumatic systems is blockages within the pipelines, where bulk materials accumulate, which result in restriction or complete obstruction of flow.
This is especially prevalent when handling materials with high moisture content, cohesive properties, or irregular particle sizes.
When blockages occur, they not only disrupt operations, but also result in downtime due to required cleaning and maintenance, leading to a halt in overall operation.
To mitigate blockages, businesses must carefully assess their material characteristics and ensure the pipelines’ design accounts for flow dynamics.
Properly selecting conveying velocities, air-to-material ratios, and pipeline diameters can reduce the likelihood of material accumulation. Unsure of how to address this? Contact MACTEX Sdn Bhd for detailed consultation and troubleshooting.
• Energy Inefficiency and High Operational Costs
Pneumatic conveying systems require positive pressure air or vacuum technology to transport materials, which can be energy-intensive, if not optimised properly.
When systems are not optimised, they consume excessive energy, leading to higher operational costs.
To address energy inefficiencies, businesses should conduct regular energy audits and troubleshooting to identify areas where power consumption can be reduced. This includes:
- Implementing variable frequency drives (VFDs) to regulate air supply based on demand can lead to significant energy savings.
- Ensuring that pipelines are properly sealed and that the blowers are operating at optimal efficiency can minimise unnecessary power usage.
- Upgrading to modern, energy-efficient conveying technologies to provide long-term cost reductions and sustainability benefits.
• Excessive System Wear and Maintenance Requirements
Wear and tear are inevitable in pneumatic conveying systems, especially when handling abrasive materials, such as minerals, ceramics, or chemical powders.
Over time, constant friction can degrade pipelines, valves, and rotary feeders, leading to frequent breakdowns and costly maintenance requirements.
As the saying goes, “Prevention is better than cure.” Therefore, preventive maintenance is crucial to extending the lifespan of pneumatic systems.
Industries should implement routine inspections to detect early signs of wear and replace worn components before they cause significant damage.
Using wear-resistant materials for pipelines, such as ceramic-lined or polymer-coated surfaces, can help reduce erosion and prolong system durability.
Additionally, installing monitoring sensors can provide real-time data on system performance, allowing for proactive maintenance and minimising unexpected downtimes.
At MACTEX Sdn Bhd, clients are supported with comprehensive maintenance services for efficient and reliable pneumatic conveying systems, as well as system upgrades to adapt to evolving operational needs.
• Material Segregation and Inconsistent Flow Rates
Certain materials are prone to segregation during pneumatic conveying, meaning that fine particles separate from coarser ones, leading to inconsistent flow rates and uneven material distribution during the material transport.
This challenge is particularly relevant in industries that require precise material composition, such as food processing, pharmaceuticals, and chemicals.
To prevent material segregation, companies should optimise system design to maintain uniform flow patterns.
Using controlled feeding mechanisms, such as rotary airlocks and discharged aids, can help regulate the movement of materials and prevent uneven distribution.
Additionally, adjusting air velocity and pressure settings ensures that materials are conveyed at a consistent rate, reducing the risk of segregation-related inefficiencies.
• System Downtime and Production Delays
Unplanned downtime due to system failures or maintenance issues can have a significant impact on production schedules and profitability.
Pneumatic conveying systems that are not properly maintained or optimised may experience frequent breakdowns, leading to costly interruptions in material handling processes.
To minimise system downtime, industries should implement predictive maintenance strategies using advanced monitoring technologies. IoT-enabled sensors, for example, can detect pressure drops, temperature fluctuations, and air leakage, providing early warnings of potential failures.
Scheduled maintenance routines, coupled with data-driven insights, also allow for quick troubleshooting before they escalate into major disruptions.
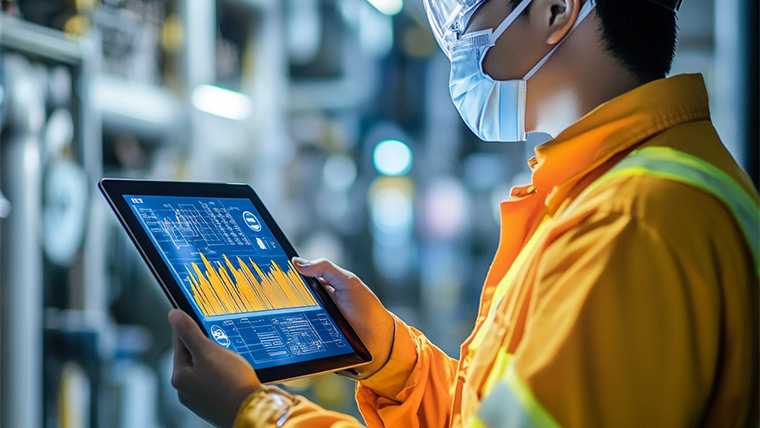
Solutions to Overcome Pneumatic Conveying Challenges
• Implementing Preventive Maintenance Programmes
A well-structured preventive maintenance programme is one of the most effective ways to ensure the long-term reliability of pneumatic conveying systems.
Regular inspections and troubleshooting, component replacements, and system cleanings help reduce unexpected failures and prolong equipment lifespan.
Businesses should develop a maintenance schedule tailored to their system’s specific requirements, ensuring that all critical components receive timely attention.
• Upgrading to Advanced Pneumatic Conveying Solutions
Technological advancements in pneumatic conveying solutions have led to more efficient and reliable systems. MACTEX Sdn Bhd leverages innovative technologies to streamline automation processes, making them cost-effective and accessible for all.
Upgrading to modern equipment with energy-efficient features, wear-resistant components, and automated monitoring capabilities can significantly improve system performance.
Investing in high-quality rotary valves, optimised air control units, and advanced filtration systems enhances operational efficiency and reduces long-term maintenance costs.
• Optimising System Design and Configuration
Poorly designed conveying systems are more prone to inefficiencies and material flow issues.
Working with experienced pneumatic system specialists, such as MACTEX Sdn Bhd, can help industries design optimised layouts tailored to their material handling needs.
Properly configuring air pressure, velocity, and pipeline routing ensures smooth material movement, reducing the risk of blockages and inconsistencies.
• Advantages of Optimised Pneumatic Conveying Systems
When businesses invest in well-maintained, energy-efficient pneumatic conveying systems, they experience numerous benefits that enhance operational success.
• Increased Efficiency and Productivity
Optimised pneumatic systems enable faster, more reliable material transport, reducing processing times and improving overall output.
Businesses can also meet higher production demands without the risk of delays caused by system inefficiencies.
• Reduced Downtime and Maintenance Costs
When preventive maintenance measures and upgrading system components are implemented, unplanned downtime can be significantly reduced.
Fewer breakdowns mean lower repair costs and uninterrupted production schedules, ultimately improving profitability.
• Enhanced Cost Savings and Energy Efficiency
Energy-efficient pneumatic conveying systems consume less power, reducing utility costs and environmental impact.
Businesses that adopt sustainable material handling solutions align with global green initiatives while benefiting from long-term cost savings.
Overcoming Pneumatic Conveying Challenges for Long-Term Success
Pneumatic conveying systems are essential for efficient material handling, but as with every material handling tool, they come with challenges that can impact productivity and costs.
By addressing blockages, energy inefficiencies, and maintenance demands through preventive strategies and system optimisations, industries can maximise the effectiveness of their conveying systems.
MACTEX Sdn Bhd specialises in providing advanced pneumatic conveying solutions designed to overcome industry challenges.
With innovative system designs, energy-efficient technologies, and expert consultation, MACTEX Sdn Bhd helps businesses achieve smoother operations, reduced waste, and long-term cost savings.
Discover how MACTEX Sdn Bhd can provide tailored pneumatic conveying solutions to optimise your material handling efficiency today.